The expansion of affordable air travel has revolutionised society and indicators predict an ever-increasing demand. Hybrid electric power is the environmentally-friendly future of long-range flight. These new engines call for radically miniaturised turbines and the components that govern the efficiency of the whole engine are the high-pressure turbine castings.
High-pressure turbine castings are manufactured as nickel superalloy single crystals and the focus of ARCANE. Our Prosperity Partnership will develop the underpinning scientific understanding and tools needed to design and develop new generations of the components that define the environmental impact.
These components are critical to the competitiveness of Rolls-Royce’s future engines. ARCANE will establish the methods to leverage naturally arising anisotropic material properties to their full advantage whilst de-risking their manufacture.
Advances and innovations in engineering, materials and manufacturing of the modern gas turbine aeroengine will continue to sustain growth in the sector whilst reducing environmental impact. By 2050 R-R aircraft and aeroengine manufacturers will fulfil their commitments to FlightPath 2050, reducing CO2 emissions by 75% per passenger km. This transformative advance requires a paradigm shift in market strategy – electrification of flight – alongside the understanding and capability to design and manufacture increasingly complex turbine components to underpin electrification. The ambition set out by ARCANE is at the heart of Rolls-Royce plc future research and development strategy.
Objectives of ARCANE
Within ARCANE we have three top-level objectives:
- Minimising sources of bicrystals by advancing our understanding of the science of their mechanisms of formation and using new knowledge to reduce scrap of existing and future components;
- Understanding the effects of crystal anisotropy on properties and developing models that allow us to design components of optimised performance through manipulation of crystal orientation; and
- Developing methods and tools to predict the location, extent and effects of residual bicrystals to underpin robust design of future generations of turbine SX components.
These will be realised through five work packages supported by machine learning and artificial intelligence.
Please come back soon to read more about our research team and for first views of our research results.
Partners
Rolls-Royce plc
University of Birmingham
University of Oxford
University of Greenwich
More about our research
Nickel superalloy single crystals
Nickel superalloy single crystal (SX) castings operate in the very hottest parts of the modern jet engine and define the environmental and cost impact. They are manufactured using an advanced form of the lost wax casting process.
Lost wax-, or investment-, casting is much valued for the detailed replication in metal of features formed on a wax ‘pattern’. A pattern is produced that replicates the desired metal form and subsequently coated, or invested, by a ceramic material or materials that will form the mould. The wax is melted away forming a cavity in to which the molten metal is poured. Rolls-Royce plc is at the forefront of this differentiating high-value manufacturing technology that other nations strive to master.
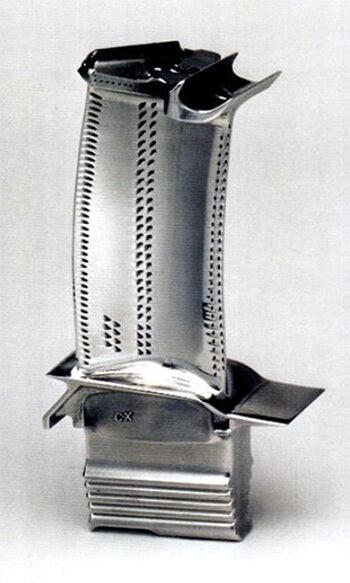
A SX superalloy turbine blade of this kind has some astonishing performance characteristics, such as:
- Operating in a gas stream ~ 200 to 300 ºC above the melting point of the alloy (think of conserving an ice cube in an oven!)
- Each blade generates up to 900hp (equivalent to a Formula 1 car)
- Using ‘cooling’ air at ~ 700ºC
- Rotating at more than 12,000rpm with blade tip speeds up to 1,200mph
- Carrying 10 tonnes of load – like suspending a double decker bus from each blade tip!
- … and yet it lasts up to 5,000,000 flying miles before it needs replacing
In SX superalloy castings their performance is dominated by the crystallographic integrity of the solidified material. Controlled solidification of >1024 atoms produces a single crystal turbine blade that is both state of the art and highly regulated (International Traffic in Arms Regulations).
To achieve the SX structure, instead of freezing metal in a mould all at once, it instead solidifies by slowly moving from a region of a furnace above the melting point to one below. Furnace technologies are highly developed to avoid breakdown of the advancing SX solidification front, but occasionally castings contain a second grain. These form via a mechanism known as heterogeneous nucleation, wherein an apparently randomly arising second grain forms and grows in competition with the main grain.
Almost all bicrystals are not fit for function in aeroengines. As turbine components are miniaturised for the hybrid electrification of flight even the smallest secondary grains become proportionally larger and more significant to performance and their formation and impacts on properties better understood.
Whilst heterogeneous nucleation events may appear random, they remain physically controlled mechanisms. Contrary to research into casting of engineering alloys to promote nucleation, our interest lies in the opposite; identifying the underlying material and process factors controlling formation of secondary grains, and then innovating to realise anti-nucleation conditions during SX casting. Rather than developing a single solution, we must understand and develop approaches that address all active and potential mechanisms of nucleation during SX casting.
Grain boundaries
When there is more than one grain in a blade the atoms at the boundary between the two – the grain boundary – cannot form the regular bonding patterns that exist within the crystal. Added to that the microstructure formed local to the boundary is also different.
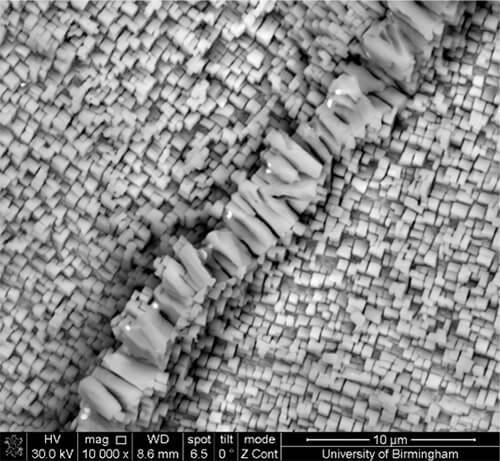
Unsurprisingly, the properties of the grain boundary are degraded compared to those of the individual grains. Why this is and how we can minimise the effect needs to be understood. But preferably we can understand the mechanisms of secondary grain formation, and by doing so develop methods to prevent them.
Mechanisms of secondary grain formation
There are at least five mechanisms that can lead to formation of bicrystals during SX casting. These are summarised schematically in the diagram. Here, we see representation of the ceramic mould material to the left, the solid growing and advancing upward within the liquid as dendrites and below the crystal lattice that can deform in an unusual manner under the action of stresses.
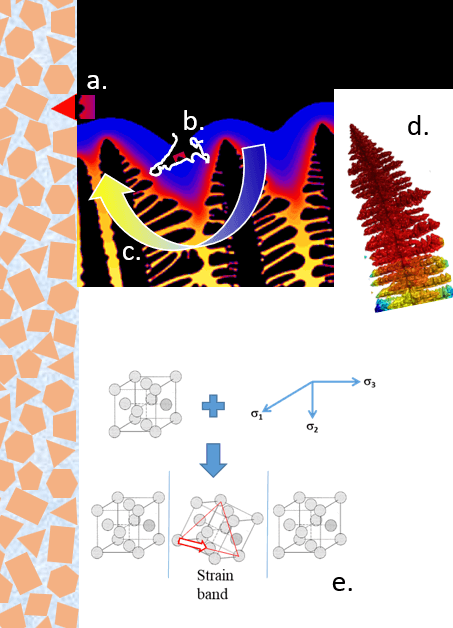
a. Reaction between the metal and an impurity in the mould.
b. Oxide films contained within the liquid metal that affect how the crystal grows.
c.The action of flow of fluid within the solidifying alloy changing local solidification conditions.
d. Creep of the solid during solidification under the action of it’s own mass causing it to deflect locally relative to neighbouring dendrites.
e. The action of stresses arising from cooling after the end of solidification.
In the above mechanisms, a and b are considered to be mechanisms that lead to proliferation of grains by formation of a new nucleus of solid. In metallurgy nucleation is the point at which a new material phase begins to form – such as a solid from a liquid - the nucleation effects in ARCANE. By this definition mechanism c is not strictly nucleation, but instead separation of solid under the action of fluid flow creates a new isolated crystal that may grow at the same time as the grain from which it was isolated. We are interested in the conditions that lead to these small fragments of solid both forming and then transitioning to sustained growth.
Mechanisms d and e arise as a consequence of mechanical effects that may be complicated further by crystal anisotropy (explained below) – the crystal anisotropy in ARCANE – or deformation at temperatures above the solidification point, a region in which material properties are poorly defined or understood.
Presently the relative importance of each of the above is unknown and unpredictable, often determined by a combination of component design and specific factors in the casting process.
Crystal anisotropy
Believe it or not, when you create a single crystal, despite the regular and repeating alignment of the atoms within it, this does do not confer properties that are uniform! Instead, when pulled or compressed in certain directions the resistance to deformation may differ by up to 2.5 times. We label such differences using the term anisotropy, and it is not just the elastic properties of the solid that are anisotropic. In fact, only by having many crystals will the properties become uniform, or isotropic, in all directions.
Anisotropy is something that can be harnessed in single crystals and allows us to ‘tune’ properties and performance under specific operating conditions within an aeroengine turbine. But, when two crystals arise within a component there arises a conflict between properties across their interface, the grain boundary, and this can lead to rapid deterioration in performance. The exact magnitude of the loss in properties is determined by many factors, not just the relative orientations of the crystals.