AMPLab team
Leadership
Lead
Professor of Advanced Materials Processing
Director of Research and Knowledge Transfer
School of Metallurgy and Materials
Professor Moataz Attallah holds a chair in advanced materials processing. He received his PhD in metallurgy and materials science from the University of Birmingham (2007), BSc (highest honours) and MSc degrees from the American University in Cairo (AUC) Egypt, in mechanical engineering, and materials/manufacturing engineering respectively. Following his PhD, Moataz worked as a research fellow at ...
- Telephone
- (+44) (0) 121 414 7842
- Email
- m.m.attallah@bham.ac.uk
Research fellows
There are no results that match your search

Research Fellow
School of Metallurgy and Materials
Abdelmoez Hussein has a PhD in material science, from the University of Oviedo, Spain, March 2017. His research has focused on magnetic materials and their applications in magnetic refrigeration and magnetic sensing.
In December 2017, he joined the University of Birmingham, school of Metallurgy and Materials as a research fellow in the advanced materials processing lab (AMPLab) until present. In ...
- Email
- a.a.m.a.hussein@bham.ac.uk

Post-doctoral Research Fellow
School of Metallurgy and Materials
Parastoo received her bachelor’s degree in Pure Chemistry from Tehran University. Afterwards, she continued her studies at the University of Birmingham, where she obtained her master’s degree in Biochemical Engineering and PhD in Tissue Engineering of bone and cartilage. After her PhD, Parastoo joined the AMPLab group to explore the applications of 3D printing in tissue engineering ...
- Telephone
- 0121 414 6803
- Email
- p.jamshidi@bham.ac.uk
There are no results that match your search
Operations and support
Kathleen Waldron
Project Support Officer
PhD students
Bonnie Attard
Francesco Careri
Francesco is a PhD student at the University of Birmingham conducting his research with TWI Ltd through the EPSRC CDT in Topological Design and the National Structural Integrity Research Centre (NSIRC). His project is focused on the development of Additive Layer Manufacturing technology as a potential means to produce thin features and more efficient Al-alloys heat exchangers for aerospace applications.
Francesco obtained his MSc degree in Mechanical Engineering at the University of Calabria in Italy. During his final year project, he collaborated as a visiting student at the AMP lab, where he carried out experimental and numerical analysis of different post-processing strategies for Ni-superalloys structures fabricated using Direct Energy Deposition.
Email: fxc017@student.bham.ac.uk
Publications
F. Careri, S. Imbrogno, M.M. Attallah, K. Essa, D. Umbrello, Finite Element Modeling of Machining Nickel Superalloy Produced By Direct Energy Deposition Process, Procedia Manufacturing, 47 (2020) 525-529. https://doi.org/10.1016/j.promfg.2020.04.120.
F. Careri, S. Imbrogno, D. Umbrello, M.M. Attallah, J. Outeiro, A.C. Batista, Machining and heat treatment as post-processing strategies for Ni-superalloys structures fabricated using direct energy deposition, Journal of Manufacturing Processes, 61 (2021) 236-244. https://doi.org/10.1016/j.jmapro.2020.11.024
F. Careri, D. Umbrello, K. Essa, M.M. Attallah, S. Imbrogno, The effect of the heat treatments on the tool wear of hybrid Additive Manufacturing of IN718, Wear, 470-471 (2021) 203617. https://doi.org/10.1016/j.wear.2021.203617
F. Careri, S. Imbrogno, D. Umbrello, J.C. Outeiro, A.C. Batista, A Residual Stress Prediction of Machining IN718 Produced by Direct Energy Deposition, Procedia CIRP, 102 (2021) 13-18. https://doi.org/10.1016/j.procir.2021.09.003.
Tugrul Talha Ersoz
Tugrul started his PhD in October 2021 with AMPLab at the University of Birmingham. His study topic is 3D Printing of Superconductors. The main objective of his research is to optimize the additive manufacturing and post-processing parameters in order to obtain a functional superconductor.
Tugrul received his bachelor’s degree in Metallurgical and Materials Engineering from Middle East Technical University in June 2015. Then he started working in the automotive industry dealing with the R&D projects, IATF 16949 quality management system establishment and OEM customer representative as a quality manager. At the same time, he continued with his master’s degree in Nanotechnology and Advanced Materials at Selcuk University and obtained his degree in July 2018.
LinkedIn Profile
Dina Fouad
Dina has recently joined as a PhD Student in the Advanced materials processing Laboratory (AMPLab) at the school of Metallurgy and Materials funded by the EPSRC Centre of doctoral training (CDT) in topological design, University of Birmingham. Dina is working on the topological design and microstructural control of additively manufactured porous Ti-6Al-4V structures. She is investigating the potential of tailoring the microstructure of Ti-6Al-4V intricate topological lattice structures fabricated by the laser powder bed fusion (L-PBF) technique as means of improving the structural and functional requirements of biomedical orthopedic implants.
Dina Fouad graduated with a BSc and MSc in Mechanical Engineering from the American University in Cairo (AUC), where- for the later-she was awarded the Medhat Haroun Scholarly Excellence award (2018) for Best Masters dissertation at AUC and the national prize for best engineering masters dissertation awarded by the Egyptian Supreme Council of Universities (2020). In her master’s research, Dina evaluated the material properties processed by a novel and provisionally patented severe plastic deformation technique known as the “Multi-Channel Spiral Twist Extrusion”. The novel technique produced enhanced material properties that have a promising application for dental implants.
Publications
- Fouad,D.M., El-Garaihy,W.G., Ahmed,M.Z., Albaijan I., Seleman, M.S. & Salem, H.G.(2021). Grain structure Evolution and Mechanical properties of Multi-Channel Spiral Twist Extruded AA5083. Metals, 11, 1276. https://doi.org/10.3390/met11081276.
- Fouad,D.M., Moataz,A.,El-Garaihy,W.G., & Salem, H.G.(2019). Numerical and Experimental analysis of multi-channel spiral twist extrusion processing of AA5083. Materials Science and Engineering A, 764. https://doi.org/10.1016/j.msea.2019.138216.
- Fouad,D.M., Moataz,A.,El-Garaihy,W.G., & Salem, H.G. (2018). Multi-Objective of Multi- Channel Spiral Twist Extrusion Process using a Response Surface Approach and finite Element Analysis. MS&T 2018: Conference Proceedings.
- Fouad, D.M.,El-Garaihy, W.G., M.M.Z. Ahmed & Salem, H.G.(2018). Influence of multi- channel spiral twist extrusion (MSCTE) processing on structural evolution, crystallographic texture and mechanical properties of AA1100. Material Science and Engineering A, 737, 166-175. https://doi.org/10.1016/j.msea.2018.09.039.
- El-Garaihy, W.G., Fouad,D.M. & Salem, H.G. (2018). Multi-Channel Spiral Twist Extrusion (MCSTE): A Novel Severe Plastic Deformation Technique for Grain Refinement. Metallurgical and Materials Transaction A, 49, 2854-2864.
Book chapters
Conference presentations
- Multi-objective Optimization of Multi-Channel Spiral Twist Extrusion Process Using a Response Surface Approach and Finite Element Analysis. MS&T conference, 2018, Columbus, Ohio, USA.
- Multi-channel Spiral Twist Extrusion (MCSTE)-A Novel Severe Plastic Deformation Method: A Numerical and Experimental study. ICMSE-RAC,2018, Egypt.
- Multi-stages Spiral Twist Extrusion: A Novel Severe Plastic Deformation Technique for Bulk Nanostructured Materials. TMS,2017, San Diego, CA., USA.
Further information
Google Scholar profile
LinkedIn profile
YouTube video
Peter Ibrahim
Peter is a first year PhD student at AMPLab, University of Birmingham. He is a Scholarship holder from the British Council in Egypt to look into the use of metal additive manufacturing in medical implants. To achieve this, he is optimizing L-PBF process parameters for printing super-elastic biocompatible titanium alloys, investigating best heat treatments and other post processing procedures needed to get required mechanical properties that mimics the actual body different tissues. One step further, he is studying the application of lattice structures into bone implants and their effect on tuning the mechanical properties of the implants, motivating osteointegration and remodeling of tissues.
Having a mechanical design background, Peter could model tissue-implant interaction for different implant designs and lattice structures. Moreover, tissue remodeling through healing process could be simulated to optimize implant designs for better healing.
Publications
• P. Ibrahim, O. Nassar, M. Arafa, and Y. Anis, “On adjusting the rotary inertia of a cantilever-type energy harvester for wideband operation,”, X International Conference on Structural Dynamics, EURODYN 2017 Procedia Eng., vol. 199, pp. 3422–3427, 2017. https://doi.org/10.1016/j.proeng.2017.09.488.
• Ibrahim, P.; Arafa, M.; Anis, Y. An Electromagnetic Vibration Energy Harvester with a Tunable Mass Moment of Inertia. Sensors 2021, 21, 5611. https://doi.org/10.3390/s21165611.
• Salem, H., Ibrahim, P., Attallah, M., and Salem, H. (February 16, 2022). "Effect of Oxygen Diffusion During the Post-Processing of Ti6Al4V Lattice Structures Fabricated by the SLM Process." ASME. J. Eng. Mater. Technol. Doi: https://doi.org/10.1115/1.4053870.
Weihuan Kong
Emily Lewis
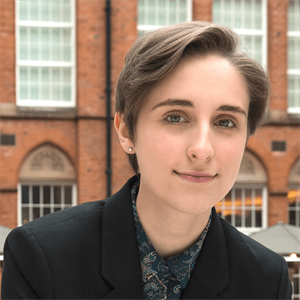
Emily is in the second year of her PhD at the School of Metallurgy and Materials, University of Birmingham. She is working with the Manufacturing Technology Centre (MTC) to investigate the additive manufacture and oxidation performance of Ni-based superalloys. For this, she is investigating Laser Powder Bed Fusion (L-PBF) as a potential means of producing Inconel 625 components. Her expertise lies in the microstructural characterisation of Ni-based superalloys at high temperatures.
Emily graduated from the University of Birmingham in June 2020 with an MEng in Nuclear Engineering, where she was awarded the Institute of Materials Prize for her dissertation on the microstructural characterisation and oxidation of Ni based superalloys.
Conference presentations
- E. R. Lewis , M.M Attallah, S. Cruchley, N. Cruchley, ‘Microstructure and Oxidation of Laser Powder Bed Fused IN625’, EPSRC & SFI International Student Conference in Metallic Materials, UK, July 2021. Winner of the ‘Best Oral Presentation Prize Award’ in the category of Advanced Processing and Characterisation.
Publications
- E.R. Lewis, M.P. Taylor, B. Attard, N. Cruchley, A.P.C. Morrison, M.M. Attallah, S. Cruchley, ‘Microstructural characterisation and high-temperature oxidation of laser powder bed fusion processed Inconel 625’, Materials Letters, Volume 311, 2022. https://doi.org/10.1016/j.matlet.2021.131582.
Anastassia Milleret
Anastassia Milleret is a PhD student with AMPLab where she is working on 4D printing of Magnetic Shape Memory Alloys. Anastassia’s research focuses on ferromagnetic materials exhibiting a plastic reversible transformation under a magnetic field, in particular, NiMnGa for Defence applications.
She qualified with an MEng in Mechanical Engineering and Materials sciences from the University of Technology of Belfort-Montbéliard (UTBM) in France. She continued her studies by spending one year at Bauman Moscow State Technical University, where she researched the nanostructures of multi-layered materials produced by cold rolling.
Upon completion, she went on to study at UTBM where she received a double diploma in Processes and Materials in partnership with the École Nationale Supérieure de Mécanique et des Microtechniques (ENSMM) and the University of Franche-Comté, in France. She worked on the printability of CoCrFeNi High Entropy Alloy by “in-situ” laser powder-bed fusion. Her final year project at Amolf institute in Amsterdam was researching bistable hinge of pneumatic pouches and auxetic materials.
Daniel Porter
Dan has just finished his first year of his PhD at the School of Metallurgy and Materials, University of Birmingham. He is working with industry partners such as DSTL and Alloyed to help with the discovery, processing, and characterisation of reactive structures. For this, he has investigated a novel laser shock plume analysis method for measuring material reactivity in a lab-based environment. He has also investigated the general microstructure of new reactive materials and is hoping to investigate the applicability of Selective Laser Melting (SLM) to the manufacturing process.
Dan graduated from the University of Warwick in 2020 with an MEng in Mechanical Engineering being awarded a 1st Class with Honours. He has industry experience in Computer Aided Design (CAD) and is keen to develop his skills further in a metallurgy and materials context.
Kun Sun
Kun Sun is a PhD student with AMPLab. Kun’s research focuses on improving the magnetocaloric properties of Ni-Mn based magnetic shape memory alloys by optimizing the process parameters of Laser Powder Bed Fusion and heat treatment processes via both experimental and numerical methods.
He obtained his bachelor's degree in Material Processing and Control Engineering at the Taiyuan University of Technology in September 2015. Then he was recommended for postgraduate studies and continued his master’s study at the South China University of Technology where he studied welding and wire arc additive manufacturing technology. He obtained his MSc degree in Mechanical Engineering at the South China University of Technology in May 2017.